Understanding High Pressure Die Casting Manufacturers
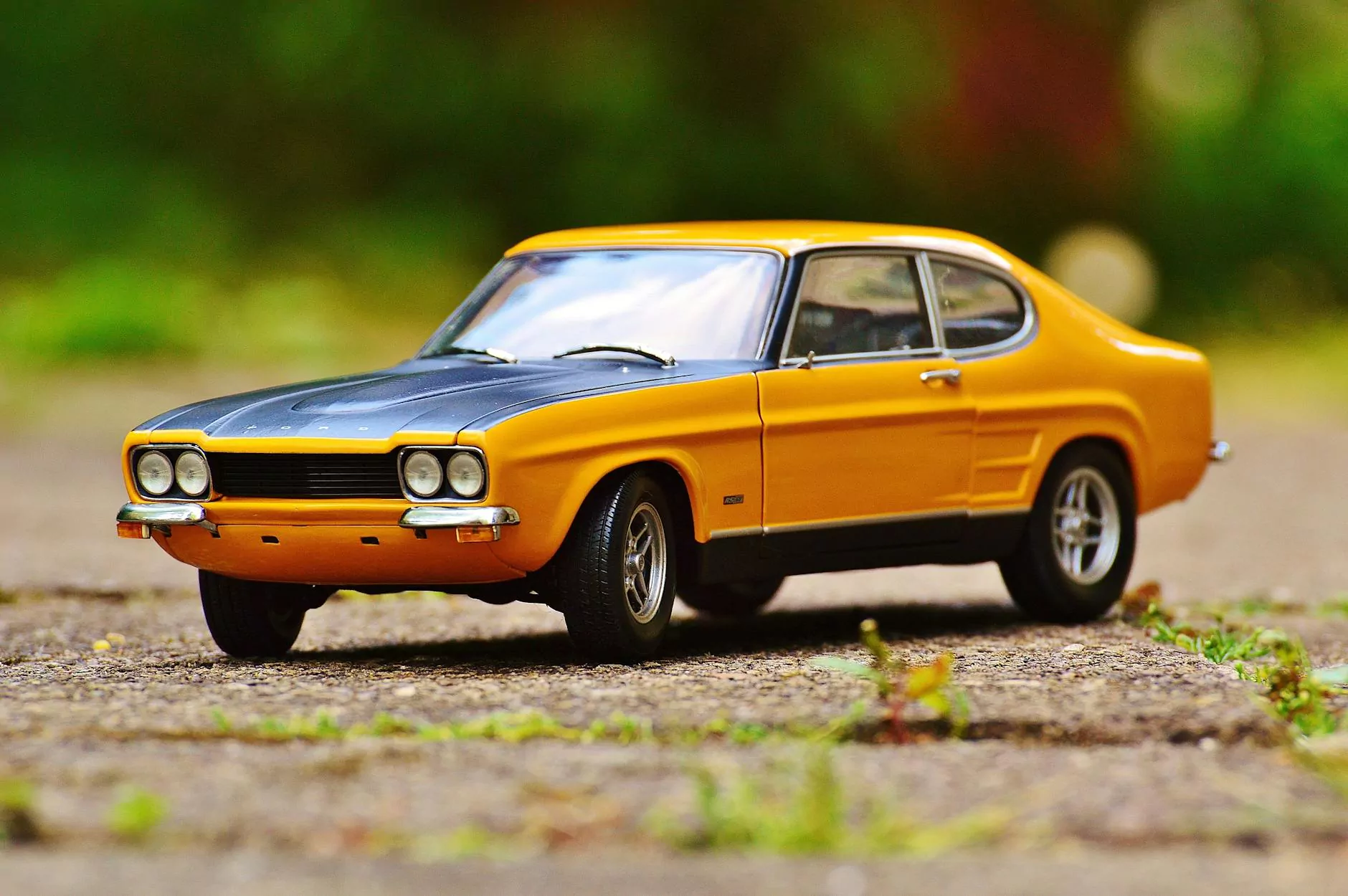
In the realm of metal fabrication, high pressure die casting manufacturers play a pivotal role. This advanced manufacturing process enables the creation of precise and intricate metal parts that meet the rigorous demands of various industries, from automotive to aerospace. In this article, we will explore the world of high pressure die casting, the benefits it offers, the manufacturers involved, and why this technology is essential for modern engineering solutions.
What is High Pressure Die Casting?
High pressure die casting (HPDC) is a method that involves forcing molten metal into a steel mold (die) at high pressure. The process is renowned for its ability to produce parts with excellent surface finishes and tight tolerances. The key advantages of HPDC include:
- Precision: Parts produced through HPDC have remarkable dimensional accuracy.
- Complex Designs: This method allows for the manufacturing of complex geometries.
- High Production Rates: HPDC is ideal for large-scale production runs.
- Material Efficiency: Minimal waste of raw materials is achieved.
The Die Casting Process Explained
The die casting process can be broken down into several key stages, including:
- Preparation: The metal is heated to a molten state, typically between 700°C to 800°C.
- Injection: The molten metal is injected into the die at high pressure, ensuring that every nook and cranny is filled.
- Cooling: The metal cools and solidifies quickly within the die.
- Ejection: Once cooled, the finished part is ejected from the die.
- Trimming: Any excess material is removed, ensuring the part meets specifications.
Key Benefits of Working with High Pressure Die Casting Manufacturers
Choosing to partner with high pressure die casting manufacturers presents numerous advantages, including:
1. Cost-Effectiveness
High volume production can significantly reduce the cost per unit. The efficiency of the process allows manufacturers to keep production costs low, making it a highly economical choice for businesses.
2. Quality Control
Reputable manufacturers implement strict quality control measures. This ensures that every produced part adheres to industry standards, enhancing product reliability and safety.
3. Versatility in Material Selection
HPDC can be applied to a variety of metals including aluminum, zinc, and magnesium. This versatility allows manufacturers to choose the best material for their application's specific requirements.
4. Rapid Prototyping Capabilities
Manufacturers can swiftly produce prototypes, enabling businesses to test and iterate designs quickly. This accelerates product development and time to market.
Industries Benefiting from High Pressure Die Casting
The impact of high pressure die casting spans across various industries:
Automotive Industry
In the automotive industry, HPDC is widely used to produce engine blocks, transmission cases, and other critical components. The precision and durability of die-cast aluminum parts significantly contribute to vehicle performance and safety.
Aerospace
Aerospace components require components that are not only lightweight but also strong and durable. Manufacturers utilize HPDC to create essential parts that meet stringent aerospace standards.
Electronics
The electronics industry frequently utilizes HPDC for producing casings and structural components for various devices. The ability to create intricate shapes and excellent surface finishes is vital for modern electronics.
Consumer Products
Metal components in consumer products often benefit from die casting. Manufacturers of appliances, tools, and gadgets heavily rely on HPDC for its efficiency and precision.
Quality Assurance in High Pressure Die Casting
Maintaining high standards of quality is essential for high pressure die casting manufacturers. Several methods are employed to ensure the integrity of the final product:
- Non-Destructive Testing (NDT): Techniques like ultrasonic and X-ray testing can identify internal defects without damaging the component.
- Dimensional Inspection: Laser scanning and other technologies ensure parts meet specified dimensions.
- Material Composition Analysis: Spectrometry and other analytical methods verify that the correct materials are used.
- Surface Finish Checking: The smoothness and finish of parts are assessed to meet aesthetic and functional requirements.
Future Trends in High Pressure Die Casting
As technology evolves, so do the processes within high pressure die casting. Here are some emerging trends:
1. Automation and Industry 4.0
The integration of automation and smart technologies is revolutionizing HPDC. Manufacturers are adopting advanced robotics and machine learning systems to enhance efficiency and reduce human errors.
2. Eco-Friendly Practices
With sustainability becoming paramount, manufacturers are exploring environmentally friendly practices. This includes the recycling of die cast materials and reducing waste through optimized processes.
3. Enhanced Materials
Innovation in metal alloys is leading to the development of new materials that are lighter, stronger, and more resistant to corrosion, further expanding the applications of HPDC.
4. Growing Demand for Customization
As industries seek more tailored solutions, the need for customized die-cast products is increasing. Manufacturers who can provide customization while maintaining cost-effectiveness will thrive.
Choosing the Right High Pressure Die Casting Manufacturer
Selecting a reliable high pressure die casting manufacturer is crucial for the success of your project. Here are several factors to consider:
- Experience: Look for manufacturers with extensive industry experience and a proven track record.
- Certification: Ensure the manufacturer holds relevant certifications that guarantee adherence to industry standards.
- Capabilities: Evaluate their technical capabilities, including design support, prototyping, and post-production services.
- Client Testimonials: Research feedback from previous clients to gauge reliability and quality of service.
- Support Services: Check if they offer design assistance and value-added services such as assembly and finishing.
Conclusion
High pressure die casting manufacturers are essential to the modern manufacturing landscape. Their ability to produce high-quality parts efficiently and cost-effectively makes them invaluable partners to various industries. By understanding the nuances of this process, businesses can leverage the advantages of HPDC to drive innovation and remain competitive in a challenging market.
It is clear that with advancements in technology, a focus on sustainability, and a commitment to quality, the future of high pressure die casting is bright. As industries continue to evolve, the demand for high-precision components will only increase, solidifying the role of HPDC in the manufacturing ecosystem.